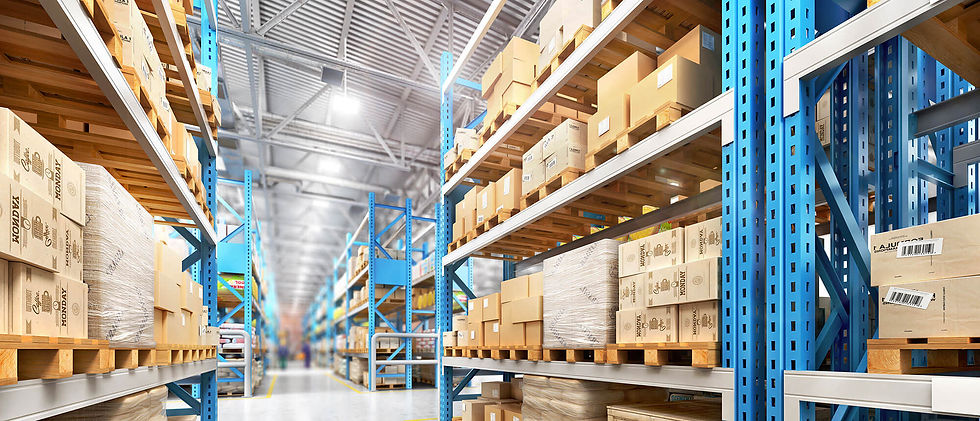
Changes in customer behavior over the last few years have created huge fluctuations in how goods are distributed this is due to supply and demand issues which have crippled supply chains over the last few years. This has led to a decrease in consumer demand, leaving businesses with an excess of inventory at every point in their supply chain.
Those quick changes in pace have made it more critical than ever for businesses to have visibility into their fulfillment operations. They need to know where have inventory and were it can be moved to ensure that they are able to adapt to changes in the supply chain.
Historically the ad hoc nature of systems running across multiple supply chain partners have increased complexity and costs in fulfilment. To provide a higher level of operational excellence and reliability the industry must invest in more optimized fulfilment technology.
What is Fulfillment Technology
Fulfillment technology is a broad technology it can be any combination of software, hardware and other technologies used to manage the process of order fulfillment, simply put it is the technology of the warehouse that gets your products from the internet to the your home or place of business. The average North American Warehouse is 25,000sq ft of space. At Brunswick International we have at our disposal a warehouse of over 60,000sq ft of warehouse that we are able to utilize to its fullest, this ensures that our warehouse is amongst the most productive and efficient in Liverpool by utilizing our warehouse Management System.
What improved operational excellency means for our customers
Our goal is to provide the very best fulfilment services for our customers. By improving overall operational efficiency, we reduce lead times for our customers, improve shipment visibility and improve cost efficiency.
Reduced lead times and improved order fulfilment accuracy. A single WMS allows us to streamline processes and optimise workflows, so orders are processed quickly and accurately. Since this system will be rolled out across all our fulfilment centres, we can achieve a higher rate of order fulfilment accuracy and reduced lead times regardless of where a customer’s orders are fulfilled.
Greater visibility. By using a single WMS across our facilities, we’re standardising the data we collect and, therefore, the visibility we offer customers. Our WMS captures data for order fulfilment and stock movement through barcode scanning, mobile app data collection, automation and other technologies, ensuring data is up to date with each action, so customers can make data-informed decisions in real time.
Scale meets customisation. By implementing a single fulfilment solution, we’re able to cover both day-to-day operations and sudden-scale large volume events like ecommerce promotions. We’re also standardising the way we offer customisable and flexible solutions, offering standard integrations with hundreds of ERPs, marketplaces, couriers and material handling equipment.
Cost efficiency. The less waste we have throughout the supply chain, the more cost efficient it is for both us and our customers. Take, for example, variable fulfilment rates. The cost of fulfilment goes up when trade volumes are high. But by improving our operational excellence, our customers benefit from more consistent rates due to improved productivity and efficiency.
Four predictions for the future of fulfilment tech
While we’re making great strides in our operational efficiency by using a single, standardised WMS, there are many more gains to be made in fulfilment technology. We have four key predictions for how fulfilment tech will evolve in the near future.
1. The operator experience and customer satisfaction will be more closely linked
Recognising the crucial link between employee experience and customer experience, the future of fulfilment tech will prioritise more intuitive interfaces that give operators a better user experience. By leveraging better design, automation, AI-powered suggestions and advanced training tools, companies can empower their workforce, leading to higher efficiency and productivity and improved customer outcomes. Investing in the employee experience and enabling seamless collaboration will be pivotal in achieving exceptional service quality.
2. Fulfilment providers will strive for an ultra-reliable, Amazon Prime-like experience
As consumer expectations continue to evolve, businesses are racing to provide better and better experiences. As a result, they expect their fulfilment partners to keep up by providing an “Amazon Prime” like experience. Reliability will become the key deliverable and fulfilment providers will have to ensure orders are processed accurately, shipped promptly and delivered on the dot. To achieve this high level of dependability, fulfilment providers of all kinds will have to leverage advanced technologies such as real-time inventory tracking, optimised routing and predictive analytics.
3. More universal design systems will lead to more fluid job roles
Universal design principles are now de facto for consumer-facing platforms, but often B2B enterprise software doesn’t implement user-centric design (think of how easy it is to use Netflix or Amazon vs. how easy it is to use expense management or HR system at work). The future of fulfilment tech will bring the implementation of more usable, universal design principles, which will enable workers to transition seamlessly between different types of jobs within the fulfilment process. This flexibility not only enhances operational efficiency but also empowers workers to become versatile contributors, ultimately leading to smoother operations and improved productivity.
4. Beyond visibility: technology-driven recommendations and actions
While visibility remains crucial for customers, the future of fulfilment tech will go beyond simple monitoring and tracking. The focus will shift towards advanced technologies that provide actionable insights and intelligent recommendations. By harnessing the power of artificial intelligence, machine learning and data analytics, fulfilment systems will be able to proactively identify bottlenecks, predict demand fluctuations and suggest ways customers can optimise their fulfilment strategies. This proactive approach empowers businesses to make data-driven decisions, automate routine tasks and continuously improve operational efficiency.
Ensuring that you partner with a Freight forwarding partner like Brunswick International Freight ensures that you will be able to move your freight efficiently and and effectively keeping ahead of the competition, ensuring that the greater returns on any new Markets you seek to exploit, so by partnering with Liverpool's number 1 Freight Forwarding business get in touch today to help your business grow to even greater heights.
Comments